ABOUT US

Dongte steel=Professional service + Reasonable low price + High quality assurance.
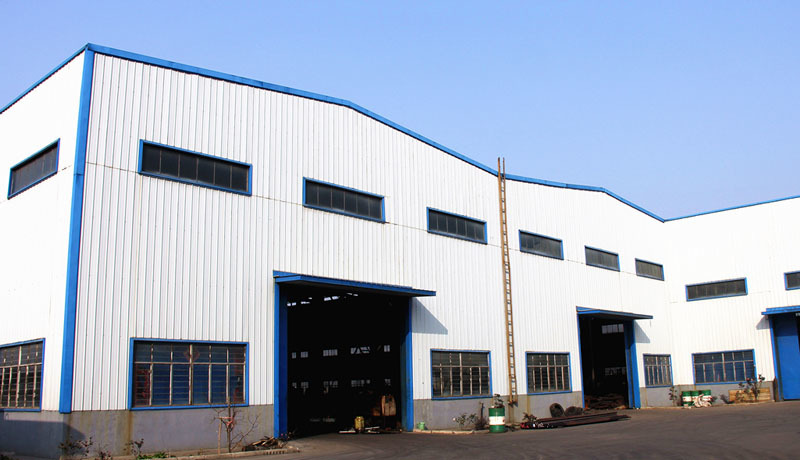
Why Dongte steel is unique?
Dongte steel is a leading manufacture for special steel in China, which was established in year 2012. Mr Wang is the owner of this company, who had been worked in Dongbei special steel mill for around 20 years before having his own business, with his professional background and strictly quality control system and management, all the materials that can meet DIN, AISI/ASTM, JIS and GB standard and had been exported to many countries, our main markets are Europe, USA, Southeast Asia, Mid East, South American and South Africa. Dongte steel had been worked with several leading companies since the beginning till now, quality had been widely accepted by customers.
More than 30 years of industry experience
Satisfied customers
NEWS

The impact of aluminum alloy materials on engine performance is multifaceted, mainly reflected in the following aspects: Lightweight: Aluminum alloy has a lower density, about one-third that of cast iron, so using aluminum alloy can significantly reduce the weight of the engine. Lightweight helps to reduce the weight of the entire vehicle, thereby reducing fuel consumption and improving fuel economy. For every 10% reduction in vehicle weight, fuel consumption can be reduced by 6-8%. Thermal conductivity: Aluminum alloy has good thermal conductivity, which can quickly transmit the high temperature and pressure generated by the engine. This helps to ensure the stability and safety of the engine, prevent thermal overload and local thermal stress concentration. Corrosion resistance and oxidation resistance: Aluminum alloys have excellent oxidation and corrosion resistance, and can maintain good stability in harsh environments such as high temperature, high pressure, and humidity. This helps to extend the service life of the engine and reduce the frequency of maintenance and replacement. Wear resistance and fatigue resistance: Aluminum alloy materials have better wear resistance and fatigue resistance compared to cast iron, and can maintain good performance under long-term high-speed operation and heavy load conditions. This helps to improve the durability and reliability of the engine. Optimizing combustion chamber design: Aluminum alloy materials have good plasticity and processability, which can meet the design requirements of complex engine structures. By optimizing the design of the combustion chamber, the combustion efficiency of fuel can be improved, further enhancing the power and economy of the engine. In summary, the impact of aluminum alloy materials on engine performance is mainly reflected in aspects such as lightweight, thermal conductivity, corrosion resistance and oxidation resistance, wear resistance and fatigue resistance, and optimization of combustion chamber design. These advantages help improve the performance, economy, and reliability of engines, and promote the sustainable development of the automotive industry.
MORE →In addition to special steel, key components of engines may also use the following materials: Cast iron: Cast iron is a common material for engine components, mainly used for manufacturing cylinder blocks, cylinder heads, and other components. Cast iron has high thermal stability and good mechanical properties, which can withstand high temperature and high pressure environments during engine operation. Aluminum alloy: Aluminum alloy is commonly used in the manufacturing of engine cylinder heads, pistons, and other components due to its lightweight and good thermal conductivity. Aluminum alloy materials can reduce the weight of engines, improve fuel economy, and have good corrosion resistance. Titanium alloy: Titanium alloy is a high-performance material with high strength, low density, and good heat resistance. In engine components, titanium alloy can be used to manufacture components in high-temperature areas, such as turbocharger blades and shafts. Ceramic materials: Ceramic materials have excellent high-temperature resistance and wear resistance, and can be used in certain key components of engines, such as valve seats, combustion chambers, etc. The use of ceramic materials can improve the thermal efficiency and durability of engines. Composite materials: Composite materials are composed of two or more materials with different properties, which have excellent mechanical properties and temperature resistance. In engine components, composite materials can be used to manufacture complex structural components, such as intake manifolds, fuel injectors, etc. It should be noted that the material selection of engine components depends on the specific application scenario and requirements. Different materials have their own advantages and limitations, therefore, in the process of engine design and manufacturing, it is necessary to comprehensively consider factors such as the working conditions, performance requirements, and economy of the components.
MORE →The specific application of special steel in engine components is very extensive, involving key components of the engine. The following are some specific applications of special steels in engine components: Crankshaft and camshaft: The crankshaft and camshaft are the core components of the engine, responsible for converting the reciprocating motion of the piston into rotational motion, and controlling the opening and closing of the valves. These components need to withstand extremely high pressure and torque, thus requiring the use of high-strength and wear-resistant special steel for manufacturing. Gears and bearings: Gears and bearings are key components in engines that transmit power and rotational motion. Special steel, due to its high strength, wear resistance, and corrosion resistance, is often used to manufacture these components to ensure smooth and efficient engine operation. Cylinder liner and piston: The cylinder liner and piston are key components of the engine combustion chamber, which need to withstand high temperature, high pressure, and high-speed motion environments. The high-temperature strength and corrosion resistance of special steel make it an ideal material for these components. Valves and valve seats: Engine valves and valve seats control the entry and exit of fuel and air, which have a significant impact on the performance and efficiency of the engine. Special steel is often used in the manufacturing of these components due to its excellent wear resistance and corrosion resistance. Turbocharger: A turbocharger is used to increase the intake pressure of the engine and increase its power output. Special steel is often used to manufacture key components of turbochargers due to its high strength and high-temperature resistance.
MORE →Special steel, as a high-performance metal material, has a wide range of applications. The following are some of the most widely used fields of special steel: Aerospace field: Special steel has very important applications in the aerospace field. Due to the strict requirements for materials in aerospace, special steel needs to have low density, high strength, high stiffness, and good heat resistance. With its excellent mechanical and heat resistance properties, special steel has become an indispensable material in the manufacturing of aircraft, missiles, satellites, and other aerospace. Automotive industry: Special steel is also widely used in the automotive industry. In modern automobile manufacturing, special steel is widely used in the manufacturing of body structures, engines, transmissions, chassis and other components. Special steel can improve the safety, economy, and comfort of automobiles. For example, high-strength steel can be used to manufacture the body structure of automobiles and improve their impact resistance. Petrochemical industry: Petrochemical equipment requires the use of special steel with good corrosion resistance and high temperature strength. For example, oil well casing requires the use of corrosion-resistant stainless steel to prevent drilling fluid from corroding the casing; The reactor, heat exchanger and other components of petrochemical equipment require the use of high-strength steel to withstand high temperature and high pressure working environments. Energy sector: With the increasing demand for renewable energy, special steel also has important applications in solar and wind energy equipment. Special steel with good weather resistance and corrosion resistance is required for equipment such as solar photovoltaic panels and wind turbine towers.
MORE →